低渗透油田在油气田开发中的地位越来越重要,正在成为开发的主体。目前油田多实行早期注水,精细注水是低渗透油田开采的主要手段之一。而迫于水资源的短缺和环境保护的压力,以采油污水做为精细注水水源,是实现采油污水资源化利用的必然趋势。精细注水要求水质达到《碎屑岩油藏注水水质推荐指标及分析方法》(SY/T5329—1994)推荐的A1级指标。 然而由于采油污水水质相对复杂,常规技术对精细注水水质和运行稳定性无保障,因此国内自20世纪80年代末就开始研究将膜技术用于采油污水的处理,并已证明膜分离技术在确保A1级水质方面具有明显优势。但由于膜污染的问题未能有效解决,膜技术用于采油污水处理的工程应用受到严重制约。 近年来,以有机膜分离技术为核心的低渗透油田精细注水水处理技术取得了较大的突破,并于2005年成功用于工程实践,然而这些技术为了最大程度地缓解膜污染,预处理流程都比较长。因此开发耐油污染的膜分离过程,以简化低渗透油田精细注水水处理流程,是目前的研究重点。 陶瓷膜表现出了比有机膜更好的耐油性能和膜通量,为此笔者选择了碳化硅陶瓷膜对采油污水进行中试试验,以全面考察其出水水质、耐污染性能和强化混凝过滤对膜通量的影响。 1试验部分 1.1陶瓷膜组件 试验采用加拿大爱德摩环保集团提供的多通道结构的非对称碳化硅陶瓷膜组件,组件尺寸D165mm×1100mm,过滤面积6.44m2,过流通道尺寸2mm×2mm,分离膜孔径0.02μm,膜表面镀有同等过滤精度的耐油涂层。 1.2试验装置及材料 试验工艺流程见图1,其中浓水仍然排回来水水箱,来水水箱每天向系统外排水1次。
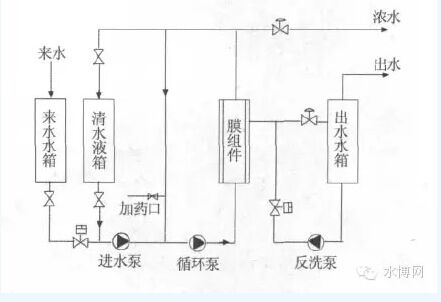
过程切换阀门采用自控开关阀或调节阀,各点设有压力、流量以及温度传感器,采用PLC自动控制系统,试验装置的运行控制参数可以通过电脑设置,可实现每10s采集1组运行数据并自动存储。PLC分别自动调整循环泵和进水泵频率,维持恒定的循环水量,控制膜表面切向流速为3m/s。 1.3试验方法 以污水处理站的气浮出水和气浮进水作为处理对象来进行试验研究。试验装置在PLC装置设定的试验参数下24h连续运行,当达到设定的跨膜压差或完成1组试验后进行化学清洗,每次化学清洗后测定1次清水(自来水)通量。定时采集各点水样进行水质检测,主要检测指标为SS、含油量、悬浮物粒径中值,根据《碎屑岩油藏注水水质推荐指标及分析方法》(SY/T5329—1994)中规定的方法检测。 1.4试验用水 试验用水来自辽河油田欢喜岭采油厂污水处理站中气浮装置的出水和进水,水温25~30℃,其中气浮出水油≤5mg/L,SS≤20mg/L,气浮进水油≤100mg/L,SS≤300mg/L。 1.5膜污染控制 在控制膜表面流速一致的情况下,分别在进水投加PAC、周期性脉冲反洗、脉冲排浓水3种方式下,对膜面的状态进行干扰,考察这3种方式对膜污染的控制情况。 1.6数据处理 膜通量(LMH)均折算为25℃和0.1MPa条件下单位膜面积的出水水量,以消除温度变化带来的误差,使不同跨膜压差下的产水量具有更加直观的可比性。 2结果与讨论 2.1进水与出水水质 试验先后采用气浮出水和气浮进水作为来水,在跨膜压差为30~70kPa的状态下运行,运行过程中长期的检测数据表明: (1)膜出水悬浮物含量与进水无关,90%以上的出水悬浮物质量浓度小于1.0mg/L,平均0.58mg/L,最大1.6mg/L。取样不规范或二次污染容易导致分析数据大于1.0mg/L。 (2)膜出水含油量与进水有关:进水中油质量浓度≤3mg/L时,出水<1.0mg/L;进水中油≤100mg/L时,出水<5mg/L;进水中油>100mg/L时,出水为1~10mg/L。试验污水采用气浮和两级多介质过滤预处理时,出水中的油可降至2mg/L以下。污水中溶解油的含量较低,因此推测污水含油量较高时,其中微小油滴或微乳液滴会变形或破裂后透过膜。 (3)膜出水悬浮物粒径中值为0.2~1.6μm,平均为0.8μm。由于悬浮物粒径中值接近检测仪器的下限,同时悬浮物颗粒的粒径小且浓度很低,因此仪器误差、随机误差及过程疏失误差等均相对较大,致使检测数据的波动较明显,采用多做平行样的方法处理。 2.2跨膜压差与膜清水通量 第一次化学清洗结束后,按一定的梯度先提高后降低跨膜压差,用清水测试考察膜通量,得到图2所示曲线。
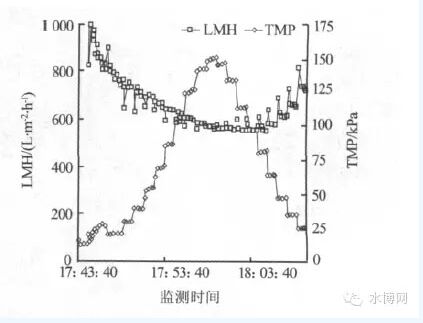
由图2可以看出,膜通量随跨膜压差的增加而下降,同时,跨膜压差下调时,膜通量较上调过程有所降低,在跨膜压差调至70kPa以下时膜通量随跨膜压差下降而上升。上述分析表明,跨膜压差的运行控制不宜出现先增加后减小的过程,且该膜组件的跨膜压差不宜高于70kPa。 2.3膜污水稳定通量与周期 在化学清洗后,且初始的清水通量基本相同的条件下,分别将跨膜压差恒定为30、70kPa,处理气浮进水,不采取附加的膜污染控制措施,对膜通量的变化进行考察,结果见图3。
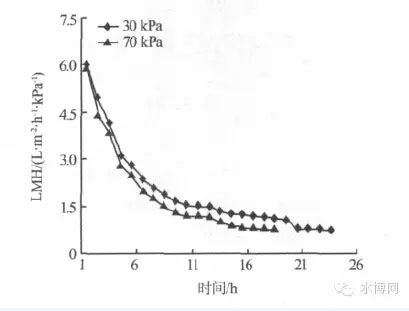
由图3可以看出,在不同的跨膜压差下,随着设备的运行,膜通量都在下降,但跨膜压差越大,膜通量的下降趋势越快。 2.4脉冲扰动对膜通量的影响 为考察脉冲扰动对膜通量的影响,处理气浮进水时,在化学清洗后投运超过4h且不采取附加的膜污染控制措施条件下,先测试了无扰动情况下膜通量的变化趋势,发现膜通量在3h内从230L/(m2•h)降到110L/(m2•h)。在初始条件相同的情况下,还进行了扰动的试验,即每7min自动进行一次脉冲排水,结果显示,在周期性扰动条件下运行,膜通量经历了从下降到恢复的周期性变化,在1.5h内膜通量基本保持不变。 2.5混凝对膜通量的影响 在化学清洗后保持基本一致的清水通量前提下,每7min自动进行一次脉冲排水,处理气浮进水,控制跨膜压差约70kPa,向进水中投加30mg/L的PAC进行混凝,考察膜通量的变化,结果见图4
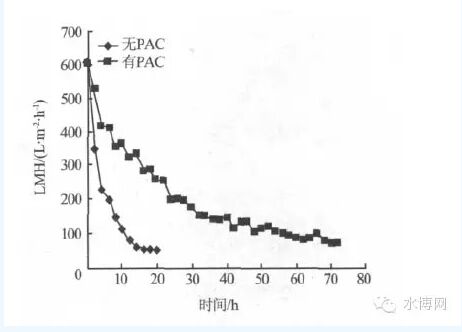
由图4可以看出,在有扰动的情况下,无混凝时膜通量的下降趋势比较快,在20h内膜通量从600L/(m2•h)降到60L/(m2•h)左右,而投加30mg/L的PAC混凝剂时,膜通量下降趋势减缓,运行70h,膜通量仍然维持在100L/(m2•h)左右。 2.6化学清洗效果 运行一段时间后,膜通量会有所下降,因此需要定时进行化学清洗。试验选用化学清洗的药剂为次氯酸钠(调到pH=12)和盐酸(调到pH=2),各清洗1h。每次清洗后均采用相同的模式测定膜的清水通量,取跨膜压差为100kPa时的通量对清洗的效果进行评估。结果表明:新膜的清水膜通量为1920L/(m2•h),运行1个周期后,膜通量降到100L/(m2•h)左右,经化学清洗后膜通量只能恢复到750L/(m2•h)。之后再经运行、清洗,与第1次化学清洗后的清水通量比较,之后清洗后的膜通量均可恢复到600~800L/(m2•h)左右,恢复率为90%~107%,化学清洗效果仍存在一定的提升空间。 3存在问题 在进水悬浮物浓度较高时维持较大的膜通量,多通道结构的陶瓷膜接近出水腔的通道,有被悬浮物堵塞的迹象,可能存在膜表面透过水量不均衡的现象。 4结论 (1)陶瓷膜处理气浮出水时可将SS和油质量浓度降到1.0mg/L以下,出水悬浮物的粒径平均可达到0.8μm。处理气浮进水时,随着气浮进水的含油量的增加,陶瓷膜处理后出水的含油量也相应增加。 (2)PAC混凝过滤可以大大缓解膜通量的衰减速率,但需要控制循环液的悬浮物含量及适宜的膜通量,或选择适宜的膜组件,避免通道被悬浮物沉积堵塞的现象,可考虑气浮或沉降-陶瓷膜组合工艺处理高悬浮物污水。 (3)对膜表面水流进行周期性扰动,可以明显减缓膜污染的速率。 (4)碳化硅陶瓷膜表面在进污水前后的外观基本一致,其耐油涂层耐油效果较好,通过化学清洗,膜通量可以在线得到较好的恢复。
|